Specialist answers from professionals
to your technical questions
By and by we will provide an overview of the most common questions posed by our customers on topics such as the optimisation of SMD stencils, solder paste printing, quick-tensioning systems, and BECKTRONIC products and services:
What means SMD?
SMD (surface mounted device).
Electrical components are soldered directly onto the printed circuit board.
What are SMD stencils?
Metal stencils made of stainless steel, fine grain or nickel material. They are used for printing solder paste on PCBs in electronics manufacturing.
With the advent of SMT technology in the mid-1980s, these print stencils were manufactured by etching, today they are usually laser-cut.
What are SMD stencils needed for?
SMD stencils, also known as SMT stencils, are used in electronics production in the area of SMT assembly (surface-mount technology) for printing solder paste onto the circuit board.
The circuit board is placed under the stencil, aligned, the solder paste applied and squeegeed over the printing area of the stencil, either manually or automatically inside the stencil printer.
What are the types of SMD stencils?
- Stencils for quick clamping frames
- Stencils in fixed frames
- Step stencils
- Maxi stencils
- Prototype stencils
- LTCC stencils
What is a step stencil?
Step stencils are SMD stencils with partially different material thicknesses. Thus, different paste volumes for different electronic components can be applied with one stencil.
What is a maxi stencil?
A maxi stencil is an SMD stencil in oversize. It is used especially for special applications.
What is a prototype stencil?
The prototype stencil is a cost-effective alternative to conventional stencils.
It is available in various sizes up to a maximum of 300mm x 200mm.
It is ideal for a PCB test run or to populate some samples.
What is a LTCC stencil?
The LTCC stencil (Low Temperature Cofired Ceramic) is a precision stencil with microscopically fine holes.
It is perfect for filling MicroVias, for mapping the finest traces or for calibrating optical systems.
What are the advantages of templates for quick release frames?
- High quality
- Very good performance at lower cost
- Suitable for volume production in addition to prototypes or small batch production
- Require hardly any storage space
These stencils are available for all common stenter frames, such as VectorGuard, QuattroFlex, ZelFlex, Metz, etc., are available.
What are the advantages of stencils in a fixed frame?
- Particularly suitable for series production
- Easy handling, even with thinnest sheet thicknesses
- Quick readiness for use
How are SMD stencils stored?
Quick-tensioning stencils and stencils in fixed frames are stored safely and space savingly on shelves. Depending on the stencil type, the storage of SMD stencils in bags or cardboard box is recommended.
For more information, see BECarchive.
How is soldering paste applied?
Solder paste is drawn over the stencils with metal or rubber squeegees. In the process, the solder paste is applied through the openings of the print stencil to the corresponding areas of the circuit board.
Which soldering process for SMD?
The common process for soldering SMD components is reflow or vapor phase soldering. In this process, the assembled boards are heated in a reflow/vapor phase oven in a controlled manner until the solder paste melts. In the subsequent cooling process, the solder hardens again and permanent and conductive connections are created. In special cases, soldering can also be carried out by selective soldering or by hand.
What are the optimal contact/landing surfaces for chip designs?
The optimal position of the component contact surface to the printed circuit board landing surface and their paste application has a significant impact on the soldering outcome of SMD components. This also applies to supposedly simple chip components. It is not uncommon for amplified soldering problems to occur here, because the size ratio or the position was not coordinated.
Optimally, the landing area should be just below the contact surface of the component. The surface should be slightly larger to the outside here to present a clean meniscus. If possible, the LP surfaces should not protrude significantly inward under the component body. The recommended values depend on the exact design or size. The 0603 design is given as an example here. Its dimensions are approx. 1.6 mm x 0.8 mm.
The appropriate landing surfaces have a size of 0.5 mm x 0.9 mm, whereby an internal distance of approximately 0.9 mm is recommended. These values promise optimal soldering results with precisely adapted paste application. Due to various factors, it is not always possible to adhere to these values. A correspondingly optimised paste application can nonetheless be achieved. At BECKTRONIC, we support you with advice and service.
What does THT mean?
Through-Hole Technology (THT) refers to a technology for making an electrical connection between components and the printed circuit board, in which component terminals are inserted and connected through pre-drilled holes in the printed circuit board.
Which soldering method for THT?
THT components are usually processed by wave or flow soldering. In this process, the bottom side of the assembled circuit board moves over a wave of liquid solder so that all contact points are wetted. In special cases, soldering can also be carried out by selective soldering or by hand.
How can a stable, reproducible lowering and contacting of QFN components be achieved?
The right paste volume is essential for an optimal soldering result. The volume connection of the "ground plane" of the exposed pad is particularly crucial. In principle, it is advantageous if the paste application of this surface exceeds the total area of the surrounding contacts by a maximum of 100%. The distribution (screening) of the paste application also plays a major role. It supports or favours the venting of flux residues. Any existing vias within the exposed pad area must also be taken in to account. Care should be taken here that no paste leaks uncontrollably to the underside during the application of paste as well as during the reflow process.
The paste application of the contact pins depends on their exact position and the condition of the edges (wetted or not wetted), and the paste is applied accordingly.
How must the stencil be layouted to correctly assemble a mix of components from 0201 to 2010 and right through to THT components?
Nowadays, it is increasingly common for a printed circuit board to consist of a wide variety of designs. Large components or structures with a high heat capacity located in the vicinity of very small designs can lead to soldering problems (thermal shading). In general, care should be taken that each design receives its own optimum paste volume. An adapted stencil layout can be used to compensate for individual mix structures.
However, if the complexity and difference in the required paste volume is too great, a stencil in step design is the tool of choice. This allows different material thicknesses to be achieved within a stencil. Each individual area can then be optimally tailored to the needs of the assembly. Since each layout is assembled differently, BECKTRONIC always advises individually and in line with customer requirements. The following decisive parameters are analysed and taken into account among other things: the component geometry, the solder stopping area, the component connection, the soldering method, the paste type, and the squeegee blade direction.
How can tombstoning be avoided?
The paste volume should be adapted to the chip design and optimised if necessary. Effective options here are surface and design adjustments. The homeplate and the bow tie have proved themselves especially useful in the past. The "bow tie" design in particular is being increasingly used. Additional attention must be paid to the position of the paste application. If a pressure offset occurs between the landing surface and the paste application, the exact positioning on the target position leads to an increased risk of tombstoning.
How can I reduce air pockets (voids)?
- Stencils:
Voids (cavities) occur when the flux has to travel a long way to the outer edge of a component surface (up to the pasting edge). In order to ensure a better, more homogeneous removal of the flux, areas (from approx. 6-8 mm²) are usually rasterised. - Solder paste:
Additionally, solder pastes with a lower proportion of flux tend to be less prone to the formation of voids. - Soldering process:
The optimisation of the soldering process with the aid of different air pressure variants (positive and negative pressure) also significantly influences void formation. This is an example of how an improved soldering result is achieved with reflow or wave soldering when nitrogen is added. The nitrogen serves as a protective gas, which reduces the oxidation of the solder and the components by oxygen. In addition, the surface tension of the liquid solder is positively influenced.
How can I prevent the "jettisoning" (popcorn effect) of components?
The reason for these are sealed cavities under components (heat dissipation in the exposed pad of a QFN) or within large paste surfaces, as well as "plugged vias", which have not been properly closed. Air pockets lead to an explosive process at this point. If the vias are not completely closed in accordance with IPC 4761 Type VI, the trapped air cannot escape and excess pressure develops under the component body. In order to counteract this process, the paste should preferably not flow into or close these sleeves during the melting process. In general, the moisture content of SMD components and printed circuit boards should also be taken into account. Otherwise, this may lead to unwanted delamination (of the LP surface) or breaking up of SMD components. An upstream annealing process (baking) can be used to remedy this.
How can I avoid the twisting or tilting of components?
Even at this point, adapting the surface paste application can be the solution. With cylindrical designs such as MELF or micro-MELF, a concave inner surface design or U-shaped paste application can guarantee secure positioning even after the soldering process. In QFN designs, reducing and rasterising the exposed pad helps to fix and evenly lower the pad.
Still have questions?
Contact person
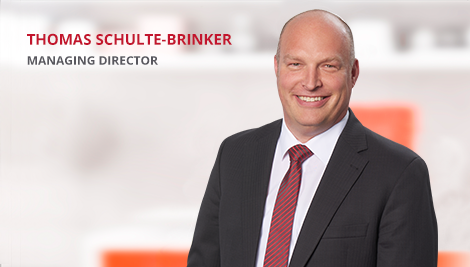

+49 2743 9204 - 15
Monday through Friday, 8 - 17 hrs
Contact form
BECnews
Subscribe now to the Becktronic newsletter for the latest industry information, news from our company, and tips and trends concerning laser-cut SMD stencils and high-precision stencils for LTCC, wafer and special applications!